La manutenzione predittiva dei cavi per reti industriali
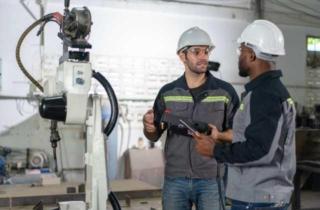
Il paradigma dell’Industria 4.0, i sensori che abilitano la Internet of Things, le applicazioni industriali dell’intelligenza artificiale e non ultima l’enfasi posta nell’ultimo periodo sull’Edge Computing, hanno fatto sì che le tecnologie informatiche penetrassero sempre più nei reparti produttivi delle aziende, con dispositivi sempre più connessi tra loro.
Insieme a tanti vantaggi, questo introduce però nuovi punti di fragilità, specialmente perché dispositivi e infrastrutture devono lavorare in ambienti aggressivi, in cui le condizioni operative sono ben lontane da quelle ideali di un data center.
Molto si è fatto per produrre pc, server e infrastrutture di rete robuste, adatte a tollerare le sollecitazioni fisiche, meccaniche e chimiche, estendendo in teoria la vita utile delle apparecchiature. Nella pratica, però, essendo ogni fabbrica diversa dalle altre, è difficile poter stimare con precisione la durata di un dispositivo, e ancor più quella di un cavo di rete, che può estendersi per decine di metri in canaline non ispezionabili ed essere sottoposto a movimenti e torsioni se collegato a parti meccaniche in movimento.
LAPP, azienda specializzata nella produzione di cavi, connettori e accessori per le reti industriali, ha sviluppato una soluzione che applica il principio della manutenzione predittiva – cioè la capacità di individuare l’imminenza di un guasto o un deterioramento prima ancora che si manifesti – al cavo stesso. Abbiamo chiesto a Simone Albrizio, Product Marketing Manager di LAPP Italia, di parlarci di questa novità.
Computerworld Italia: Perché la manutenzione predittiva dei cavi utilizzati nelle macchine industriali, catene portacavi o robot è tanto importante? Quali sono i vantaggi rispetto alla manutenzione preventiva e a quella correttiva?
Simone Albrizio: Nonostante siano stati progettati per resistere anni, i cavi utilizzati nelle applicazioni dinamiche come le catene porta cavi mobili o i robot, sono sottoposti sia a stress meccanici di trazione, di schiacciamento, di taglio, abrasione, flessione o torsione, sia a stress ambientali come temperature elevate o molto basse, la presenza di agenti chimici, oli e umidità. Questo stress potrebbe generare anomalie come errori di rete, perdita di pacchetti, instabilità di connessione tra cavo e connettore. Queste anomalie potrebbero portare al danneggiamento della guaina o dell’isolamento, con il risultato finale di costringere a un fermo macchina inatteso. Per ovviare a questo potenziale problema, gli operatori delle macchine avevano fino a oggi solo due opzioni:
- Manutenzione Preventiva: sostituire periodicamente tutti i cavi prima che possano rompersi, mantenendoli in opera per un tempo limitato. Questo comporta un notevole spreco di denaro, perché alcuni dei cavi che si sostituiscono potrebbero funzionare bene ancora per un po’ di tempo;
- Manutenzione correttiva o reattiva: sostituire il cavo solo in seguito a una sua rottura o deterioramento delle prestazioni. In questo caso, però, possono esserci danni derivanti da fermi macchina non programmati o produzione di pezzi non conformi nel periodo di malfunzionamento.
Con l’arrivo della manutenzione predittiva, promessa centrale dell’Industria 4.0. qualcosa è cambiato. La caratteristica fondamentale della manutenzione predittiva è l’intervallo di intervento dinamico, grazie al monitoraggio continuo dello stato dei componenti. Il vantaggio, rispetto a quella preventiva preventiva (intervalli fissi di manutenzione che spesso portano a «rottamazioni» di componenti buoni) e a quella correttiva (sostituzione in caso di danni e fermi macchina non pianificati) risiede nell’avere una riduzione dei costi di fermo macchina, perché si può inserire nelle finestre di manutenzione programmata per altri scopi, ed evita sostituzioni inutili.
CWI: In cosa consiste quindi la vostra soluzione?
SA: La nostra soluzione Etherline® Guard, che verrà presentato durante l’SPS di Norimberga a fine Novembre 2021, è un dispositivo in grado di monitorare e analizzare le prestazioni dei cavi di rete in tempo reale, al fine di prevederne la fine del ciclo di vita. I dati delle prestazioni vengono analizzati con il LAPP Predictive Indicator (LPI), un algoritmo che calcola la durata residua delle linee. Il sistema attinge a dataset con milioni di valori raccolti e analizzati nel centro di test LAPP e li trasmette via WI-FI o LAN al sistema di supervisione della macchina o impianto, utilizzando il protocollo MQTT.
La funzione di diagnostica si basa sul calcolo continuo dei parametri del cavo, che vengono confrontati con curve di riferimento elaborate in base all’esperienza di Lapp.
Etherline guard è dotato di due porte Ethernet ed è semplicemente collegato al cavo da monitorare. Poiché i pacchetti di dati vengono trasferiti in modo trasparente da una porta Ethernet all’altra nella modalità “cut through”, il dispositivo non è visibile dal PLC collegato e quindi non sono necessarie modifiche al software, né tanto meno ha alcuna influenza sulla trasmissione dati della macchina.
Inoltre, la soluzione di manutenzione predittiva di LAPP non richiede cavi sacrificali aggiuntivi nelle linee: ciò significa che non c’è alcuno sforzo di installazione aggiuntivo e il sistema può essere facilmente adattato alle macchine esistenti.
CWI: Quali sono i principali benefici? Ci sono già dei dati sui risultati in termini di efficienza dell’impianto, diminuzione dei fermi macchina?
SA: Il dispositivo permette di aumentare il networking e la trasparenza degli impianti, sempre più richiesta dall’Industrial Internet of Things, oltre che il monitoraggio continuo delle prestazioni e valutazione dei dati sulle condizioni per aumentare l’efficienza (Digital twin).
Una Overall Equipment Effectiveness (OEE) migliorata, grazie alle manutenzioni programmabili, che consentono di evitare fermi macchina imprevisti e quindi riduzione dei costi di gestione.
Come già anticipato, non c’è nessuna interferenza con la struttura del cavo e quindi non è neanche necessaria una costruzione speciale del cavo. È possibile installarlo come retrofit in tutti i sistemi basati su Ethernet, anche su macchine o impianti più datati.
In ultimo, i valori di soglia del sistema sono configurabili direttamente dall’operatore della macchina, e viene reso disponibile un Log file dettagliato su SD card.