LEF, la digital factory friulana dimostra le tecnologie Industria 4.0 dal vivo
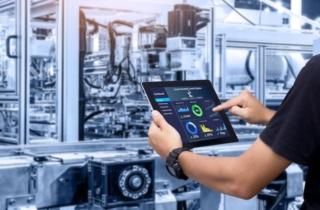
Un recente webinar di Oracle ha fatto il punto sui più recenti sviluppi della LEF (Lean Experience Factory) di San Vito al Tagliamento (Pordenone) che costituisce uno dei più interessanti casi italiani di Industria 4.0.
Nata 10 anni fa come centro di formazione esperienziale da una joint venture tra McKinsey e Confindustria Alto Adriatico, con partecipazione di altre realtà locali, la LEF è nel tempo cresciuta diventando una “azienda digitale modello” con macchine, uffici, prodotti e operatori reali (produce compressori per frigoriferi), che fa parte della rete dei nove Digital Capability Center partecipati da McKinsey in tutto il mondo.
Oggi LEF svolge anche attività di consulenza sulla gestione lean, trasferimento tecnologico e metodologico, e use case program, prestandosi come ambiente aziendale e di fabbrica reale dove validare soluzioni innovative. E qualche mese fa ha inaugurato i suoi nuovi spazi triplicati (3000 mq) con investimenti di 11 milioni, finanziati dalla Regione Friuli Venezia Giulia e da partner e fornitori di tecnologie.
A proposito di partner, Oracle è presente nella LEF con la suite completa di applicazioni Cloud Fusion ERPM, implementata nell’azienda modello friulana con il contributo del partner Alfa Sistemi, che ha partecipato al webinar insieme a due utenti Oracle (Alcar Ruote e Bormioli Pharma) e a Marco Olivotto, Managing Director di LEF.
Un “teatro d’impresa” con le complessità del mondo reale
“LEF è un’azienda reale modello, rappresentiamo in modo realistico l’intera catena del valore di un’azienda produttiva”, ha spiegato Olivotto introducendo il webinar. “È come un “teatro d’impresa” ma con tutte le complessità del mondo reale: mostriamo come implementare processi di trasformazione, con tutti i tool e tecnologie necessari. L’obiettivo è permettere a manager e imprenditori di esplorare, testare e mettere in pratica le ultime tecnologie digitali integrate con nuovi modelli di lavoro: oltre 200 aziende ogni anno vengono a farci visita”.
“Abbiamo contribuito a questo progetto, che ci ha consentito di far parte di un team internazionale, portando la nostra esperienza di 20 anni di system integration specializzata sui sistemi ERP”, ha aggiunto Federica Meroi, Sales & Marketing Manager di Alfa Sistemi. “È fondamentale poter mostrare e far toccare con mano alle aziende, e in particolare alle PMI, quanto valore si ottenga avvicinando l’ERP alla fabbrica attraverso le migliori tecnologie e applicazioni”.
Simone Marchetti, Business Development Director di Oracle, ed Elena Avesani, Global Sustainability Director di Oracle, hanno spiegato poi come tecnologie e metodologie applicate nella LEF siano cruciali sia per la competitività, anche a livello internazionale, sia per la sostenibilità. “Logistica, pianificazione della domanda e supply chain sono oggi i processi chiave”, ha sottolineato Marchetti. “Per vincere le attuali sfide di mercato, è necessario costruire il nuovo modello di impresa digitale connessa, agile e resiliente in cui la sostenibilità rappresenta un tassello imprescindibile”.
“La creazione di modelli di economia circolare, tracciabilità e trasparenza della catena produttiva sono gli aspetti fondamentali del percorso di innovazione sostenibile”, ha aggiunto Avesani. “Per le operations e i data center, Oracle sarà Carbon Neutral entro il 2025: in Europa i data center Oracle sono già alimentati con il 100% di energia rinnovabile e questo impegno si riflette anche nella tecnologia presso i clienti e partner Oracle”.
La pianificazione integra finanza e amministrazione con operations e fabbrica
Olivotto e Sergio Gimelli, ERPM Solution Consulting Director di Oracle, hanno poi accompagnato i partecipanti online in un tour virtuale della LEF, tra macchine, uffici e processi di produzione, illustrando dal vivo alcuni aspetti delle Oracle Cloud Applications utilizzati nell’azienda modello friulana: “Tutti i processi sono connessi, compresi vendite e acquisti. In particolare l’applicazione di pianificazione integra l’area finanziaria ed economica con quella operativa e di fabbrica, arrivando fino alla valutazione del rischio dei vari scenari, come per esempio l’impatto dell’arrivo in ritardo di un componente sui lead time”.
“Abbiamo la possibilità di mostrare circa 150 “use case” di produzione”, ha aggiunto Olivotto. “Abbiamo robot, collaborazione uomo macchina, sistemi machine vision per controllo qualità, il modello digitale della fabbrica con controllo real time dell’intero impianto e possibilità di drill down sulle singole macchine, e con i dati che arrivano dal campo in real time possiamo fare l’analisi predittiva di possibili anomalie e guasti, con feedback al sistema di pianificazione”.
I casi Bormioli Pharma e Alcar Ruote
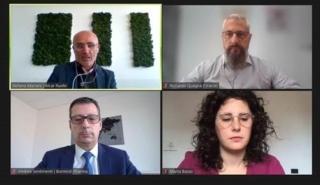
Dall’alto a sinistra: Mariani (Alcar Ruote), Riccardo Quaglia (Oracle), Sentimenti (Bormioli Pharma) e Marta Basso che ha condotto il webinar
Il webinar si è poi concluso con le testimonianze dal vivo di due clienti Oracle. “La digitalizzazione è un percorso olistico per affrontare un cambiamento culturale e rendere la struttura di business più flessibile grazie anche alla modernizzazione delle piattaforme ERP e SCM e dei sistemi di analisi dei dati”, ha detto Andrea Sentimenti, Marketing & Innovation Director di Bormioli Pharma. “Questo tra le altre cose ha permesso a Bormioli Pharma, che è leader italiano nel packaging farmaceutico, di avviare un processo di riciclo dei materiali plastici e offrire una gamma completa di prodotti riciclati”.
“Oggi nel nostro settore due fattori critici di successo fondamentali sono la capacità di risposta in tempi sempre più brevi alle richieste dei clienti, e l’ampiezza dell’offerta, che significa poter produrre lotti piccoli, mettendoli poi insieme a livello di consegne per ottimizzare la logistica”, ha detto Stefano Mariani, IT Manager di Alcar Ruote. “L’innovazione oggi può portare sia differenziazione che sostenibilità: noi stiamo puntando sulle ruote in acciaio di design, il cui ciclo produttivo produce meno CO2 rispetto alle ruote in lega leggera. Per supportare tutto questo dobbiamo introdurre sistematicamente nuove tecnologie hardware e software, e soluzioni con tempi di implementazione molto bassi, e per questo SaaS e PaaS sono preziosi. I sistemi informativi devono consentire il controllo real time dei flussi di prodotti fisici in azienda, e poi è importante la facilità di estendere e integrare soluzioni, e quella di gestire sorgenti dati molto diverse nelle fabbriche, con aggregazioni diverse per decision maker di livelli diversi”.